|
|
Capabilities of Petro Farayand Mehraz Consulting Engineers Company
Design of Flare Gas Recovery Unit
In most oil-rich countries, a significant amount of gases called flare gases are burned annually, followed by a large volume of pollutants and greenhouse gases entering the atmosphere. Therefore, most companies are trying to find a solution to this problem and economically exploit flare gases. Flare gases have economic value as they can be compressed and recovered as liquid hydrocarbon products or used as flammable gas as a process fuel or power generation. Accordingly, Mehraz is proud to contribute to reducing the pollution of the region, but also to find methods of exploiting recycled gases through a field study and to benefit from the benefits and advantages of using recycling packages..
|
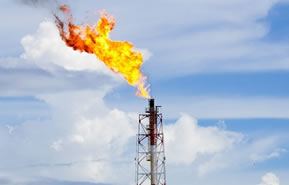 |
Gas Sweetening Unit Design
One of the most important parts of gas processing is the separation of acid gases, including carbon dioxide and hydrogen sulfide. Gases obtained from petroleum sources mainly contain varying amounts of hydrogen sulfide and carbon dioxide. Natural gas is called “sour gas” because of its bad smell resulting from its sulfur content. Sour gas is an undesirable gas and causes severe corrosion due to its sulfur content, which can be very dangerous and toxic to breathe. The sulfur in sour gas can be extracted and sold as a by-product. Petro Farayand Mehraz Consulting Engineers Company is ready to cooperate with various companies in the field of designing a gas sweetening unit.
|
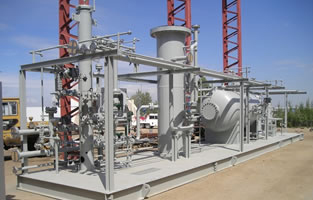 |
Natural gas Dehumidification unit Design
The natural gas flow from underground reservoirs often carries water vapor with it, and in some cases, free water is also formed with this flow. The temperature of the gas decreases as it moves from the ground to the surface due to pressure drop and conductive heat exchange with the pipe in the well and the cooler walls of the formation. Since the ability of gas to hold water vapor is directly related to temperature, the natural gas produced is almost saturated with water vapor when it reaches the surface. The further reduction in temperature of this water vapor-saturated gas will cause the formation of free water. As it cools further, hydrates are formed, which will cause serious damage to process equipment, flow restrictions, and gas transport. This is where dewatering from natural gas shows its importance..
|
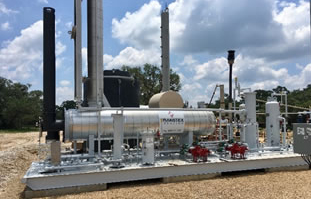 |
Gas refinery processes design
In gas refineries, it is used to purify and optimize the properties of gas extracted from operating gas wells to make the gas generally usable.
The various units in gas refineries include:
Gas and condensate reception and separation unit
Gas condensate stabilization unit
Sweetening unit
Sour gas purification unit
Dehumidification unit
Demercaptanization unit
Dew point and gas density adjustment unit for transportation
Sulfur recovery and freezing unit
Surface, industrial and wastewater purification unit
Flocculation unit
Processing unit
Pressure boosting unit
Sulfur solidification unit
Power generation unit
Industrial water desalination unit
Steam generation unit
Compressed air generation unit
Fuel gas unit
Petro Farayand Mehraz Consulting Engineers Company is ready to cooperate with various companies in the field of designing each of the above units..
|
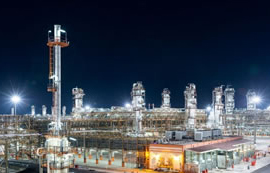 |
Waste oil treatment units design
Used oils are one of the environmental pollutants; therefore, recycling used engine oils will not only protect the environment, but also economically, it is a highly cost-effective and contributes to the recycling of waste materials and their conversion into reusable materials. At least 8 types of additives are added to produce engine oil, and these additives are obtained in the form of bitumen after recycling. In Iran, a small number of companies use the remaining asphalt from the process, and most of the treatment companies engage in unprincipled burial, which pollutes the environment while having a high economic value. Petro Farayand Mehraz Consulting Engineers Company is ready to participate in the design of engine oil treatment units, using expert engineers.
|
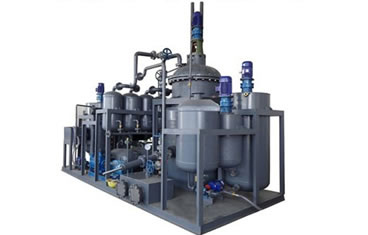 |
Chemical injection package design Oil and gas companies use chemical injection packages in exploration and recovery activities and many other processes to increase production, reduce corrosion, and separate oil/gas/water. Chemical injection packages vary greatly depending on the application, process used, number of chemicals, injection points, and changes in production and output conditions. Petro Farayand Mehraz Consulting Engineers Company is ready to participate in the design of various chemical injection packages with the help of expert engineers.
|
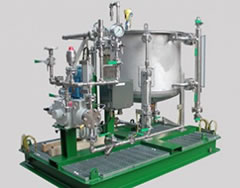 |
Bitumen production unit design
Bitumen is a hydrocarbon material that, due to its special characteristics, including impermeability to water and adhesion, has various applications, including the construction industry, coating, sealing, stabilizing quicksand, etc.
As a designer, Petro Farayand Mehraz Consulting Engineers Company has the ability to design the bitumen refining system required by various industries in accordance with the environmental conditions approved by the Environmental Organization.
|
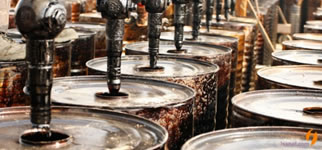 |
Desulfurization process from oil cuttings and gas condensates
Recently, regulations on sulfur content in liquid fuels are becoming more stringent worldwide because sulfur in liquid fuels, after combustion, leads to the emission of SOx and sulfate particles, which pose a risk to public health. Also, sulfur compounds in fuels cause corrosion in equipment, deactivate catalysts in refinery units, and reduce product quality.
Over the past years, many methods have been reported to remove sulfur compounds from petroleum compounds. These methods include hydrodesulfurization (HDS), biological desulfurization (BDS), adsorption processes, oxidative desulfurization (ODS), and so on.
Oxidative desulfurization is one of the promising technologies for reducing sulfur content at low temperatures and atmospheric pressure. In general, another desulfurization process is oxidative desulfurization, which consists of two stages. The first stage is the oxidation of sulfur, in which the nature of sulfur-containing compounds changes, and in the second stage, sulfur is removed during separation operations such as extraction, distillation, and absorption. In oxidative desulfurization, heavy sulfides are oxidized to sulfoxide and sulfone (without breaking the carbon-sulfur bond), respectively, by taking one and two oxygen atoms. It is worth noting that the side reaction of sulfoxide formation can be prevented by using an excess amount of oxidizing agent. Oxidation leads to an increase in the polarity and molecular weight of sulfurs, ultimately facilitating separation.
The most common industrial process used for sulfur removal is hydrodesulfurization. In this process, sulfur-containing materials present inpetroleum mixtures are converted to hydrogen sulfide in the presence of hydrogen gas and suitable catalysts, such as nickel-molybdenum on alumina (NiMo/Al2O3) and cobalt-molybdenum on alumina (CoMo/Al2O3) catalysts. Typically, the operating conditions for this process are hydrogen partial pressures between 15 and 200 psi and temperatures between 200 and 425 degrees Celsius.
The hydrogen sulfide produced by this process is converted to elemental sulfur by the Claus process. The operating conditions of the process depend on the degree of desulfurization and the range of sulfur compounds in the feed. The Claus process is the main petrochemical desulfurization process that extracts elemental sulfur from hydrogen sulfide present in natural gas and in gases produced as by-products during crude oil refining. Currently, most of the sulfur required by the world's industries is obtained in this way. In this process, a portion of the hydrogen sulfide is burned in a furnace to form sulfur dioxide, which is then reacted in the presence of a catalyst to produce elemental sulfur. |
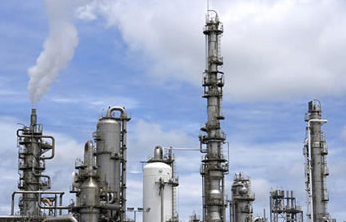 |
Industrial solvent production unit design(400 and 500 group solvents, pentane and hexane)
Petroleum solvents are light cuts that are obtained from crude oil or other hydrocarbon sources. Petroleum solvents have various applications that can be used in cases such as as a solvent for gums, paint industries, adhesives, resins, rubber and also in the food industry, oil extraction and also in some chemical reactions as a reaction medium. They are also used in the production of products of various industries and agriculture. The importance and application of these types of solvents in various industries and the strategy of converting oil into more valuable materials instead of being used solely as fuel are among the cases that increase the desire to produce and supply these solvents, which in itself can bring high added value to refining units. In refineries, naphtha is one of the most important products of refining units that is not supplied directly to the consumer. Naphtha is used in the manufacture of various solvents, as a feedstock for catalytic conversion units and as a feedstock for some petrochemical industry units. In fact, a portion of hydrocarbons that has the potential to produce petroleum solvents is a portion that is in the naphtha boiling range. Therefore, if a crude hydrocarbon source is available for the purpose of producing petroleum solvents, the source that has a higher naphtha fraction is given priority in terms of solvent production. Some of the sources that have the potential to produce petroleum solvents of the 400 and 500 groups are:
Light naphtha - This product is a product of the atmospheric distillation unit and constitutes about 4-6% of crude oil and is produced in all oil refineries. Its main uses are mixing with motor gasoline and preparing AW-406 and AW-410 solvents.
Heavy naphtha (HSRG) - Another product of the atmospheric distillation unit, its percentage relative to crude oil is about 12% and it is used in catalytic conversion units.
Blending Naphtha - This product is a product of atmospheric distillation tower and its production amount is about 4% compared to crude oil. In addition to its use in oil and gas, this product is also used as a pour point modifier in the manufacture of solvents, which are used to produce AW-402,403 solvents.
Isomax light naphtha (LIN) is a product of the Isomax unit and is produced only in refineries that have an Isomax unit. One of the distinctive features of this product is its short distillation range, and the percentage of sulfur in this product is very small. In addition to producing motor gasoline, this product is used in the production of AW-406 and AW-410 solvents. |
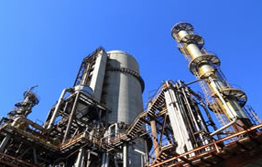 |
Design of Mini Refinery Units, Atmospheric Distillation and Vacuum Distillation
The purpose of a set of small refineries, known as mini refineries, is to refine and separate raw materials such as crude oil, gas condensate, solvents, etc. to produce valuable and high-purity materials such as naphtha, diesel, and kerosene. These refineries are designed with a capacity much lower than the capacity of conventional refineries.
Advantages of building mini refineries:
They have high flexibility in the feed input to the unit, due to problems related to the provision and diversity of raw materials
They have high profits against low investment
High speed of return on initial capital: In the first phase, the capital is returned almost the first year after the start-up.
Fast construction and commissioning
They do not depend on a specific location
As an example of these refineries, atmospheric distillation, vacuum distillation, and gas condensate distillation can be mentioned.
|
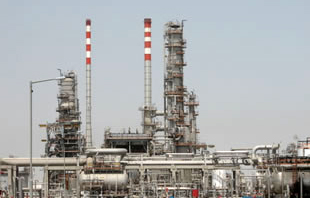 |
Gas condensate and crude oil distillation units design
Crude oil distillation is carried out in two units, first in the atmospheric distillation unit and then the residue from this unit is refined again in the vacuum distillation unit. The products of the atmospheric distillation tower are valuable products such as naphtha, gas oil, kerosene and diesel. The products of the vacuum distillation tower include heavy gas oil, light, medium and heavy lube oil, slops and vacuum bottoms. |
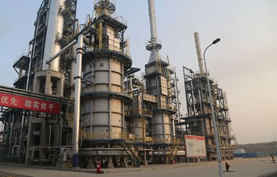 |
Base oil production unit design
Base oil can be obtained from petroleum or non-petroleum sources. Most of the base oil consumed in the world today is obtained from the refining of crude oil. Since the main basis for the production of lubricants is base oil, a major part of the use in lubricants is in addition to the production of motor oil for vehicles and also in the oil industry itself for lubricating oil industry equipment, the production of base oil is of particular importance. Oil companies receive crude oil (lube cut) from crude oil refineries and convert it into final oil (motor and industrial oil) through special processes. Mineral (or petroleum) base oils are obtained from the oil cut refining (LUBE CUT) in the oil refinery and are used in the manufacture of the majority of motor and industrial oils. Feedstock for oil companies:
Crude oil (LUBE CUT): The oil cut contained in crude oil, which is extracted from the vacuum distillation tower of crude oil distillation units as lube cut, is considered the main feedstock for oil producing companies. This product constitutes nearly 90% of the feedstock of these companies.
IsoRecycle: A by-product of IsoMax units in oil refineries that is absorbed by oil companies under the name IsoRecycle and used as part of the feedstock. The price of IsoRecycle is dependent on the price of Lubecut.
Additives: To produce different grades of motor and industrial oil, additives (depending on the grade of oil produced) are added to the base oil produced in oil factories.
Base oil for the production of finished oil, engine oil, industrial oil, extract for the production of industrial soot and rubber factories, slack wax for use in paraffin, grease and antifreeze factories are products of oil companies.
Petro Farayand Mehraz Consulting Engineers Company is proud to design a base oil Group I, II and III production units based on the most up-to-date global technologies with the above-mentioned feedstocks. |
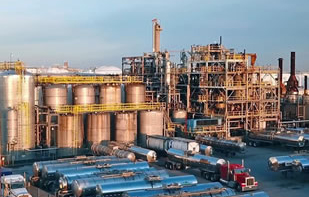 |
Crude oil Production units design
A production unit is actually a factory with all the necessary equipment where the separation of gas and oil produced from wells takes place and then the separated gas and oil are sent to the desired location. A production unit consists of various types of equipment and tools, including pipes, valves, separators, pumps, turbines, precision instruments, etc. The design of the production unit is carried out with specific criteria, taking into account the conditions of the site and the capacity and overall operational situation. Petro Farayand Mehraz Consulting Engineers Company, using the knowledge and professional experiences of its experts, designs crude oil production units with the latest versions of engineering software. |
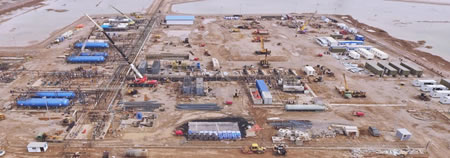 |
Oil and gas pipeline network design
One of the most important parts of an industrial unit is its inputs and outputs. The input feed and output product from a chemical and petrochemical process are supplied and sent by transmission lines. The produced stream from a hydrocarbon reservoir, depending on its type, may come to the surface through production wells in different phase conditions. In cases such as the transfer of crude oil or gas condensates within the pipeline, some water hammer conditions may be created in the pipeline, which makes it very necessary to predict the amount of waves caused by it for pipeline design. Transmission lines always travel a long distance, and modeling and simulating these transmission lines and designing them correctly is very important. Petro Farayand Mehraz Consulting Engineers Company has the ability to design transmission lines in the field of oil and gas transmission lines, utilizing the professional knowledge and experience of its experts, with the latest versions of engineering software in both the process and piping sectors. |
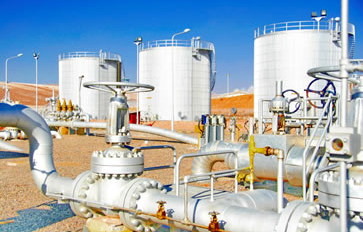 |
Crude oil desalting package design
The presence of water in oil causes the formation of salt in the oil, which if these compounds are not removed from the oil, will cause problems in the oil refining process and numerous process problems, reduce the quality of the oil and reduce its price, so one of the most important processes in oil refining is crude oil desalting. Therefore, to prevent the problems mentioned and create added value on the way out of the exploitation section and before the oil reaches the refinery, processes such as desalting are performed on the oil, the purpose of which is to reduce the amount of salt in the oil. Petro Farayand Mehraz Consulting Engineers Company, in the field of oil and gas transmission lines, using the professional knowledge and experience of its experts, in line with existing standards and guidelines, along with the latest versions of engineering software, offers the possibility and competence to perform various services in the field of designing a desalting package for desalting crude oil.
|
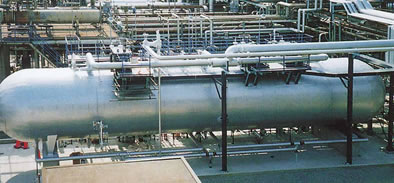 |
|
|
|